Basics of SLS for Prototyping
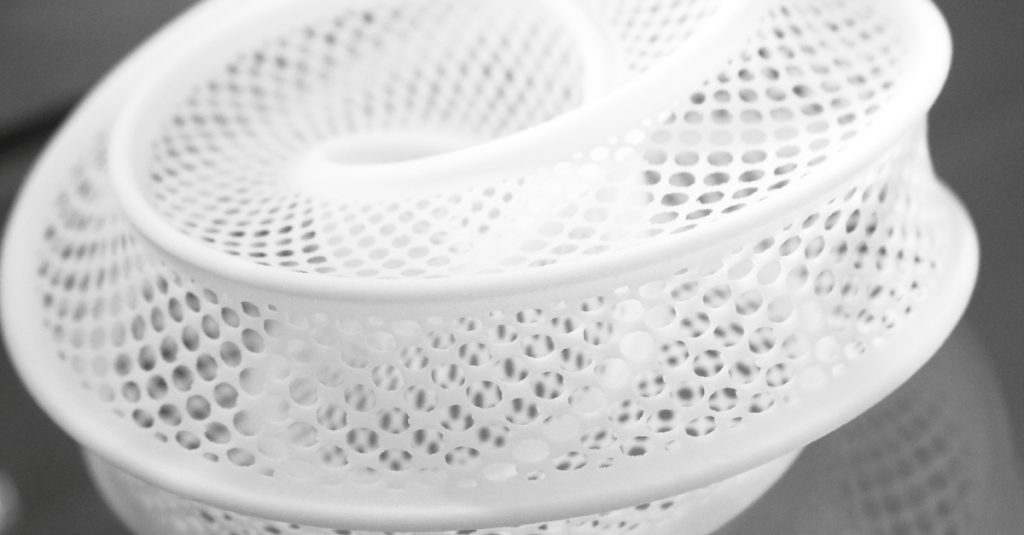
3D printing has seen a remarkable evolution, growing from basic prototypes to complex, finished products that touch nearly every sector imaginable. This shift underscores the importance of grasping the various 3D printing technologies at our disposal, each offering unique methodologies, applications, and advantages.
At the center of this technological revolution is Selective Laser Sintering (SLS), a prominent form of additive manufacturing technology that has become a preferred option due to its versatility in design and material use. As we delve into the fundamentals of SLS 3D printing, we’ll explore why it’s garnered such attention and how it compares to and contrasts with other popular 3D printing technologies. Whether you’re new to the realm of additive manufacturing or looking to keep abreast of the latest developments, understanding the basics of SLS is crucial in today’s rapidly evolving manufacturing environment.
What is SLS 3D printing
An SLS prototype is a kind of prototype made using a 3D printing technology known as selective laser sintering. This rapid prototyping technology and method is recommended and widely used for the manufacture of 3D parts that have unique geometries, complex shapes, dimensions, and/or specifications. Selective laser sintering is an additive manufacturing method that makes an extensive range of shapes and sizes possible. It also offers a wide selection of finishing options to suit different product requirements, not to mention quick turnaround, which makes SLS prototyping ideal for various applications and projects.
In selective laser sintering, a laser is used to sinter plastic material (usually powdered plastic) into a solid structure or shape, based on a 3D design or model. SLS prototype technologies have dramatically evolved over the years, making it a popular choice for product developers and engineers. In addition to quick turnarounds and the ability to produce complex shapes and geometries, SLS prototyping offers a long list of benefits, including low cost per part and high productivity levels. SLS machines can also accommodate various types of already established prototyping materials, making the technology an ideal choice for all kinds of applications, ranging from small-batch/low-volume bridge manufacturing to functional prototyping.
Selective laser sintering was among the first AM (additive manufacturing) methodologies developed in the mid-eighties. The original method engineered by doctors Carl Deckard and Joe Beaman has since been adapted to develop even more advanced technologies capable of working with a range of different materials, including composites, plastics, and even metals, ceramics, and glass. These technologies are collectively referred to as powder bed fusion technologies, which make use of processes in which thermal energy selectively sinters or fuses together different regions or layers of a powder bed. Today, there are two widely used powder bed fusion technologies and systems, known as plastic-based, SLS and metal-based DMLS (direct metal laser sintering). Selective laser melting is another term commonly used to refer to similar technologies.
An SLS prototype is created using SLS 3D printers that make use of high-power laser in order to fuse together small polymer powder particles, according to a 3D model or design. These printers fuse particles together to create a solid part.
SLS rapid prototyping: Advantages and applications
Selective Laser Sintering (SLS) has become a cornerstone in the world of rapid prototyping, standing out with its speed, efficiency, and precision. This method of 3D printing has redefined how prototypes are made and introduced a vast range of applications, stretching beyond mere prototype creation to the production of final, end-use parts.
One of the primary advantages of SLS lies in its ability to create complex geometries without the need for additional resistance structures, a feat not easily replicated by other 3D printing methods. This capability opens up a world of possibilities, allowing for the design and production of parts and products that were once deemed too intricate or complicated to manufacture.
Moreover, SLS is renowned for producing durable parts. The strength of SLS-printed items means they are not just prototypes but are robust enough to function as final parts. This durability is particularly crucial in industries where components are expected to withstand significant stress or use, ensuring longevity and reliable performance.
The application of SLS technology extends across a wide range, proving valuable in sectors such as automotive, aerospace, medical, and consumer goods. From prototyping to end-use production, its versatility is evident, making SLS a preferred choice for professionals aiming to expedite the product development process without compromising on quality.
How does an SLS 3D printer Function?
Understanding the functionality of an SLS 3D printer involves delving into the core components of the machine and the intricate processes it employs from start to finish.
At its core, every SLS machine, including models like the Formlabs Fuse 1 and other series of SLS 3D printers, operates on a similar basic principle. The process begins with a thin layer of plastic or metal powder spread across the printer’s build platform. A high-precision laser then scans the surface, selectively sintering the powder particles according to the 3D design data. This process is repeated layer by layer until the entire object is created. Each layer fuses with the one before it, gradually forming a solid part from the powdered material.
One of the key attributes of SLS printers, ranging from the first benchtop industrial systems to the more traditional industrial SLS setups, is their ability to produce parts without the need for support structures. This is because the unsintered powder acts as self-supporting material during the printing process. This distinctive feature allows for the creation of complex geometrical shapes and even moving parts within a single print run.
After the printing is completed, post-processing begins. This stage involves several steps, including cooling, removing excess powder, and then cleaning and finishing the surface of the parts. Depending on the end-use of the part, additional post-processing such as painting or sealing may be required to enhance the appearance or durability of the final product.
Despite the variances in size and complexity between compact SLS solutions and larger industrial SLS systems, the underlying process remains consistent. The printer receives the design file, typically via a wireless connection, and the user sets specific process parameters and controls. These settings can include laser speed, temperature, and layer thickness, all crucial factors that influence the quality of the final SLS part.
What is the difference between SLA and SLS in rapid prototyping?
SLA and SLS are common terms in 3D printing, but they work differently. SLA uses light to harden liquid resin into a solid shape, building it one layer at a time. On the other hand, SLS uses a laser to melt powder together to form a solid shape, also layer by layer.
When comparing SLA and SLS for rapid prototyping, several factors stand out. First, the materials used are different. SLA uses liquid resin, while SLS uses powder, which can be plastic, metal, or other materials. This difference affects the final product’s look and feel, with SLA generally achieving a smoother finish and SLS providing stronger and more durable parts.
In terms of speed, SLS might be slower in printing compared to SLA because it uses a laser to sinter powder, a process that takes time. However, SLS doesn’t need support structures, saving time in post-processing.
Both methods have their places in industrial 3D printing. SLS is great for functional parts that need to be tough, while SLA is suitable for parts that need a smooth surface or fine details.
So, the main difference between SLA and SLS is in the materials, process, speed, and the final use of the printed parts. Knowing these differences helps in choosing the right method for your 3D printing work.
Exploring the versatility of SLS materials and end-use parts
SLS 3D printing stands out in the world of additive manufacturing for its ability to work with a wide variety of materials. This technology isn’t limited to a single type of input; instead, it can print using a broad range of materials from polymers like nylon to an array of metals, granting significant flexibility in manufacturing options.
One of the key materials used in SLS is nylon, favored for its durability and versatility. SLS nylon is used to produce everything from consumer products to high-performance parts in the automotive and aerospace sectors. Beyond nylon, SLS technology is compatible with a suite of materials, including high-performance thermoplastics and composite materials, which are chosen based on the desired mechanical properties and surface finish of the final part.
The ability to print end-use parts directly without the need for molds or additional machining is where SLS truly revolutionizes manufacturing. Parts produced are ready to use or install, with properties closely mirroring those of traditionally manufactured items. This not only speeds up the production process but also significantly reduces costs, particularly for custom or low-volume parts.
Furthermore, SLS offers remarkable customization possibilities. Since items are built layer by layer from digital files, changes can be made right up to the moment of printing, allowing for a high degree of personalization and adaptation. This is crucial in sectors like healthcare, where customized parts can provide enhanced patient outcomes, or in industries where a rapid response to market changes is beneficial.
Moreover, the absence of required support structures in SLS printing means that designers can create complex internal structures, impossible to manufacture traditionally. This unique aspect allows for the printing of multiple parts within a single 3D space, maximizing efficiency and material usage.
Why use SLS? evaluating its standing among popular 3D printing technologies
When it comes to 3D printing, Selective Laser Sintering (SLS) holds a strong position due to its unique benefits and broad applicability. It’s considered one of the best 3D printing options available, especially for projects requiring durability, complexity, or a smooth finish without visible layer lines.
SLS is practical for various industries, from automotive and aerospace to medical and fashion. Its ability to create complex geometries without support, use a wide range of materials, and produce parts with excellent mechanical properties makes it suitable for both prototypes and functional products. Whether it’s for a small business looking for fast prototyping or a large manufacturer needing robust parts, SLS offers effective 3D printing solutions.
The versatility of SLS is also a key factor in its popularity. It’s not just about what you can create with SLS, but also the efficiency of the process. The additive manufacturing process involves adding material layer by layer, allowing for an economical production, minimizing waste, and offering the ability to produce only what’s needed.
Looking ahead, SLS technology shows promising potential for growth and evolution. With ongoing advancements in materials science and 3D printing technology, it’s likely we’ll see faster printing times, an expanded range of materials, and even improvements in color and finish options. Additionally, as more industries recognize the benefits of SLS, its applications are expected to expand, solidifying its place as a preferred method of 3D printing.
Conclusion
As we reflect on the expansive world of 3D printing, it’s clear that Selective Laser Sintering (SLS) plays a pivotal role in this domain. Its unique ability to turn powder materials into robust, complex structures positions SLS as a standout in additive manufacturing.
From rapid prototyping to the production of end-use parts, SLS offers unmatched versatility and precision. Its capacity to create detailed, durable components without the need for support structures simplifies the manufacturing process, enabling designers and engineers to bring even the most intricate designs to life.
Moreover, the wide range of materials compatible with SLS, from robust thermoplastics to metals, underscores its adaptability across various industries. Whether in aerospace, healthcare, fashion, or consumer electronics, SLS has proven to be a valuable tool for innovation.
Looking ahead, the potential of SLS is vast. As technology advances and more materials become available, its applications will continue to expand. Therefore, embracing SLS 3D printing isn’t just an option; it’s an avenue to pioneering design and production possibilities. For anyone committed to staying at the forefront of manufacturing innovation, leveraging the power of SLS is not just an opportunity—it’s a necessity.